An interesting little brief.
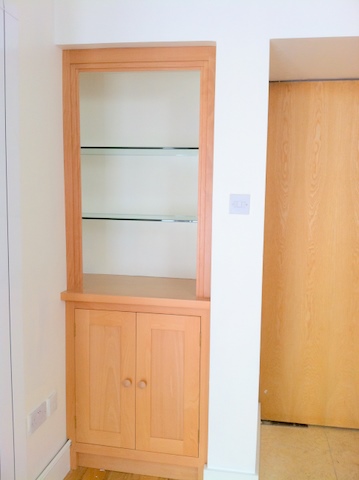
The alcove to the left of the doorway was existing.........
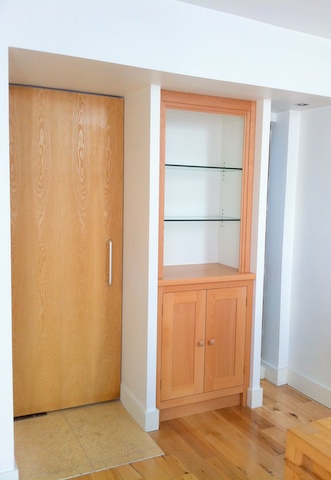
........but we created the one to the right to match and provide further storage and display space.
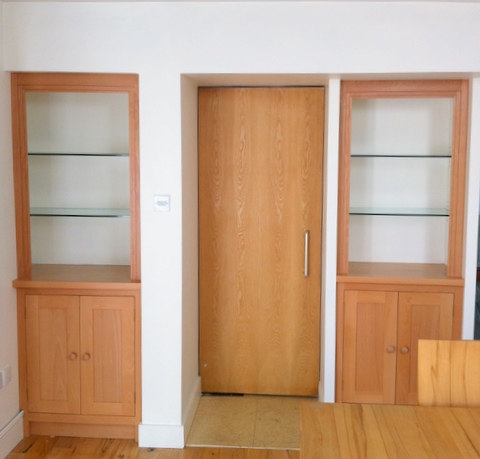
And into each alcove we introduced beech cupboards and counters beneath 10mm. toughened plate, glass shelves behind simple beech architraves.
I see that I ended my last entry in this saga, on 24 August, by writing 'I trust that by tomorrow evening I will have much more to show'.
I think I did but, plainly, I didn't show it.
And here it is now 9 September, and still I have revealed no more.
Well, the fact is that 'the item' is completed, delivered and starting its life with its new owners and in its intended surroundings!
By August 24 I had reached that moment when I needed to complete the task. - I was under no pressure from my clients but I'm afraid I am a crisis worker: it's my nature so, if there isn't pressure, I need to create it to get the adrenalin flowing!
I will leave it to your imagination as to what the 'pressure' was in this case!
So, on 25 August I got 'stuck in' and neither my work schedule nor my mindset allowed for any gaps or spaces for blogging my efforts and the progress, nor foranything else for that matter.
I worked through the weekend of 28 / 29 August and on the Saturday informed my clients that I would deliver on Tuesday morning, 31 August, to further spur myself on.
But, while I enjoyed every moment of the work, and progress was consistent and good, I decided on the Sunday that I needed one more day and informed my clients accordingly on the Monday morning.
The delivery was made on Wednesday 1 September.
Although during this last phase I was in no mood to blog, I did keep something of a pictorial record as I went, so I can now show aspects of the final stages of the project.
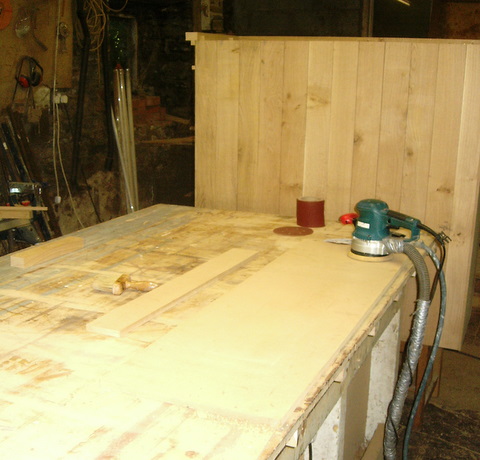
The workbench is cleared in readiness for sanding all the components shown in the last post, prior to assembly and finishing (lacquering, varnishing or polishing).
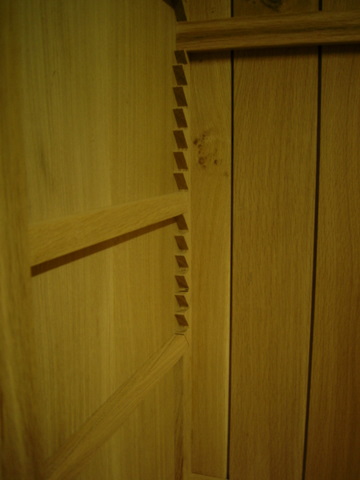
So, first, I sanded the interior of the upper. cupboard unit before sanding and fitting the traditional, oak shelf supports.
(Incidentally I decided to leave the interior of the cupboard, as well as the insides of the drawers, raw (unpolished), in the traditional manner.)
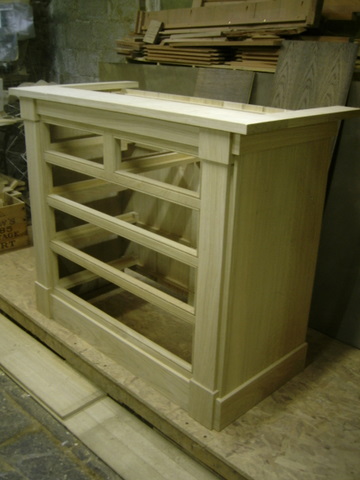
My next task was to sand and fit the heel-blocks, pilasters, skirting and frieze in the configuration agreed after the client's visit.
(Note how all the margins between these various elements have been refined from the 'mock-up' I did to help them come to a decision.)
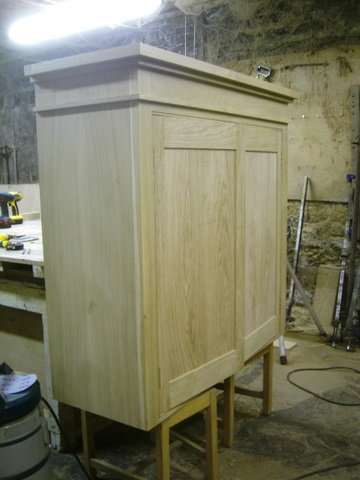
I hung the doors but, at this stage, they had not yet been brought to width.....
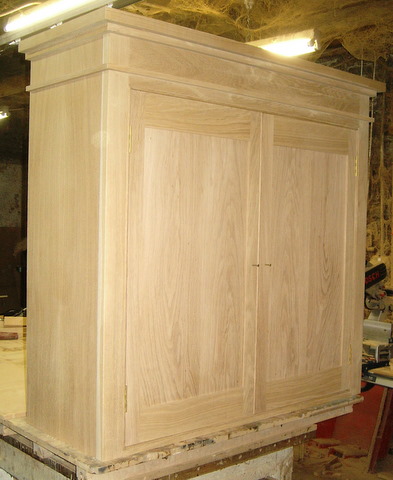

......and here they are fully fitted with good margins. (the spaces between the doors and the frame of the cabinet and the gap between the two doors)
This image shows the matching of the panels.
(The match is good but not quite as good as I had hoped.
As I showed in the second entry on this project, on 27 July, the panels are made from adjacent boards from the tree from which they were cut. In other words, when I bought them only the thickness of the saw-cut (about 5mm) separated them. However I was unfortunate in that when I planed one of them it revealed an unsightly, natural blemish so I had to keep planing until it disappeared - perhaps another 10mm - so the perfection of the mirror image diminished, marginally, with every pass over the planer.
You may further note that the panels are each made of two boards joined in the centre and it is the outer and inner boards of each door that are matched: not the two boards within one door.)
When I designed the item, I planned that the doors would be rebated - again in the traditional manner - and my colleague Martin, who got out (made) the frames allowed for this to be done. This involved making the meeting (centre) stiles (upright members) of the door frame 12mm wider to allow for the rebate (half and half overlap).
Clearly, rebated doors determine that one door has to be opened before the other door can be opened. Conventionally it is the right door that is the lead-door (the one that must be opened before the other door can be opened).
But I made a mistake! I installed the panels in one of the frames upside down.
Now, had we not allowed for rebated doors this would have been catastrophic and I would have had to remake a frame, (or both frames, because throughout the project, I paid such close attention to timber (grain) matching.)
But, by eliminating the rebate, I was able to turn the entire door, into which I had placed the panel the wrong way up, upside down, thus restoring the panel match.
Is it a down-grading of the item that it does not now have rebated doors?
That is a matter of opinion.
When I started out designing and making furniture I always rebated all meeting doors, whether in a cabinet, bookcase, wardrobe etc..
But increasingly this met with customer resistance. Many, if not most, users found it annoying that they had to open one door before they could open the other. In other words they found it irksome that they had to open the right hand door when they wanted to access something that they knew to be behind the left hand door.
Now that I have admitted my error, I wonder what my clients think?
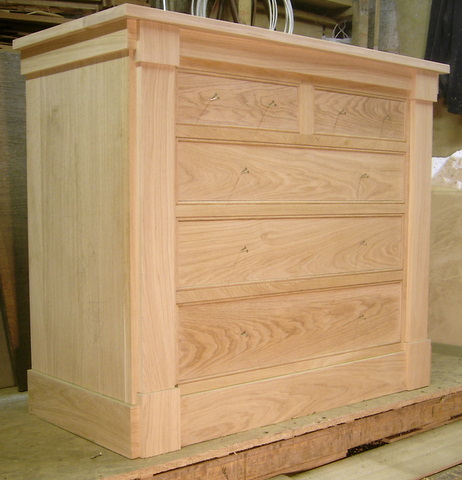
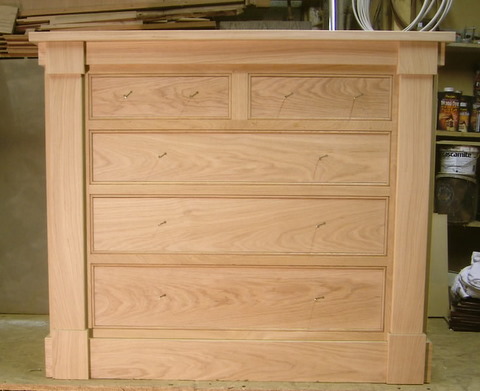
The drawers, now sanded, with screws (which cast some interesting shadows) in the positions for the knobs.
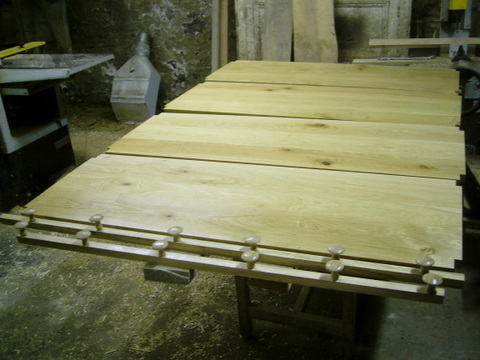
The knobs and shelves................
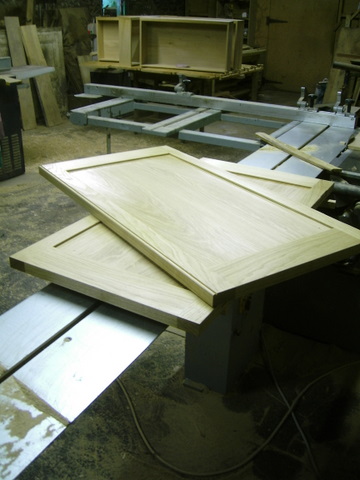
..............and the doors with the drawers in the background..............
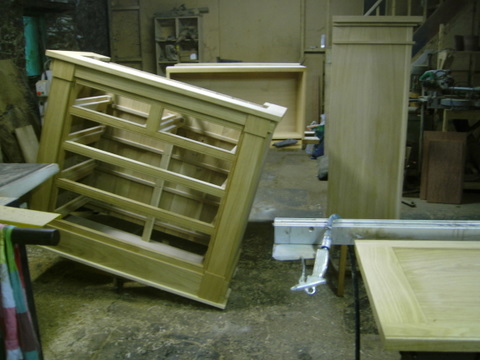
.............and the other components all back from the spray shop.
(I mentioned that the interior of the cupboard and the insides of the drawers were left raw. However, I decided that the shelves should be given a light seal-coat as I was concerned that raw oak might stain white linen, the storage of which I had been told was to be the purpose for the cupboard.)
(And the finish for the exterior of the item is a light seal-coat of 'sanding base coat' cut back (that is, sanded with very, very fine sandpaper, 360 grit, otherwise known as 'flour paper') and my own wax, 'Nunn's Beeswax and Genuine Turpentine Furniture Polish'.)
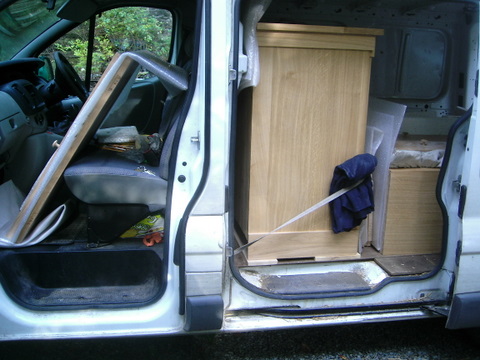
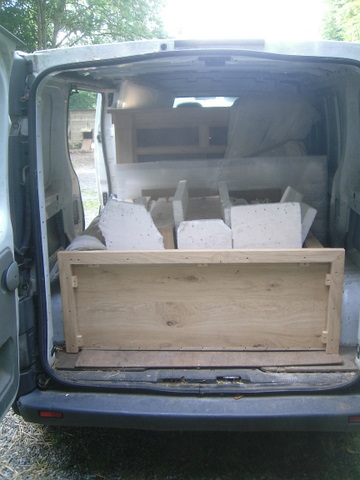
Loaded in readiness for delivery.
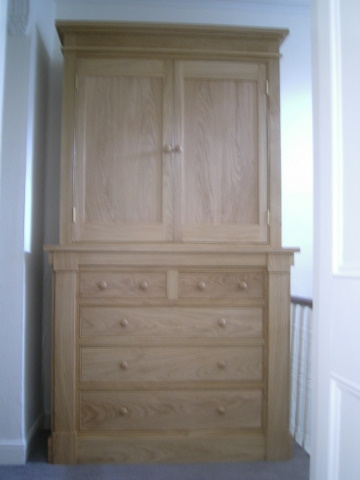
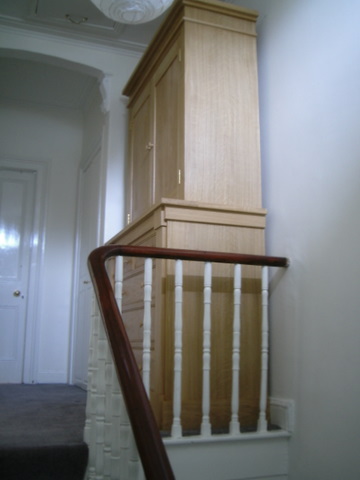
And , finally, 'in situ' in its new home!
(Unfortunately its position is such that it was very difficult for me (with my camera's rather basic lens) to take a decent picture and, also unfortunately, I was working on my own at the end of the manufacturing process and I was not strong enough to erect it in the workshop (and photograph it) before it left me.
So, close on six months after the phone rang with the initial enquiry, The Gentleman's Dressing Cupboard project is complete.
I am very pleased with it and, once the materials issue was resolved (which was time consuming and frustrating) have enjoyed almost every inch of the task.
And my clients graciously expressed their satisfaction, in fulsome terms, also.
There will be a post script to this.
Almost inevitably there will be adjustments to be made once it has acclimatized to its new surroundings: it is in the nature of solid wood furniture, especially in this age of central heating.
Also, when I sought my clients' permission to blog the 'history of their commission' I was asked if, in reciprocation, I would sign the item.
I said I would but I forgot to do so before delivery. But it will be done.
Progress has not been as good as I hoped and intended over the last ten days.
Various unforesen and extraneous matters intervened.
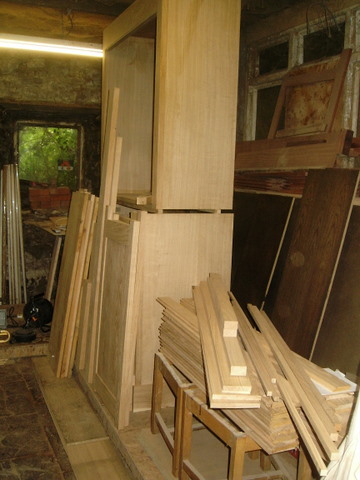
But for some time now all the components have been machined and ready for assembly.
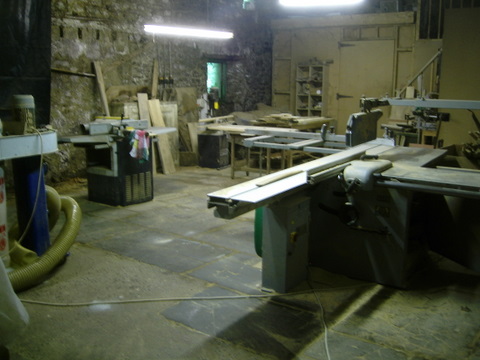
And before starting the final construction and finishing phases I decided give the machine area a long overdue clean-up.
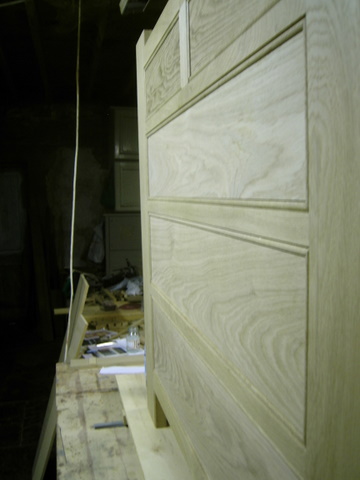
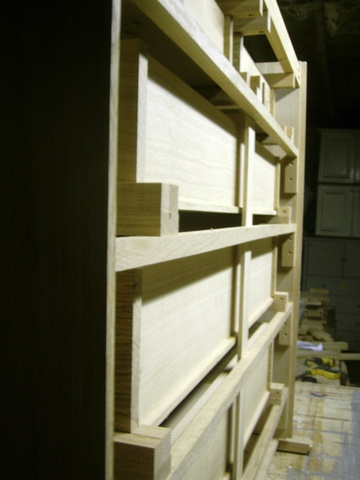
In fact we made significant progress today, but not of a particularly visual nature.
All the drawers are now fully fitted with their margins correct and their top-runners (to prevent the drawers sagging when they are pulled-out) in position.
I trust that by tomorrow evening I will have much more progress to show.
I mentioned that the next event was to be a visit from the clients' to view the work-in-progress.
Well, it took place over the weekend.
When the visit was being arranged I was told that the purpose of the visit, or a part at least, was for their children to see the item under construction.
Now, I have been making furniture for a long, long time and I have had many and many workshop visits and inspections: visits to inspect progress; make decisions and, no doubt, for clients to satisfy themselves of some doubt or anxiety; but never had the proffered purpose been ' to show the childrren'
But there is always a first in everything so, even if a little quizzical, I looked forward to the event and I was not to be disappointed for their children, one boy, one girl, one of them nine and the other twelve engaged, and were engaged, with every detail. - It transformed the usual routines of a workshop visit into a thoroughly enjoyable occasion.
.............................
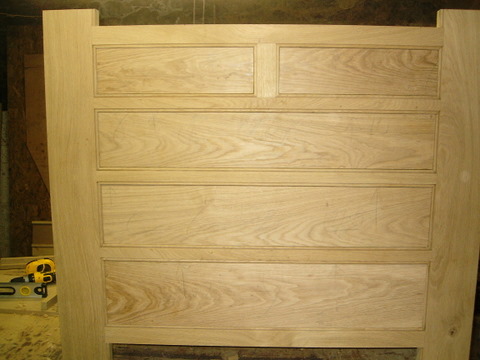
Some readers may have observed, in previous posts, the wide stiles of the chest-of drawers.
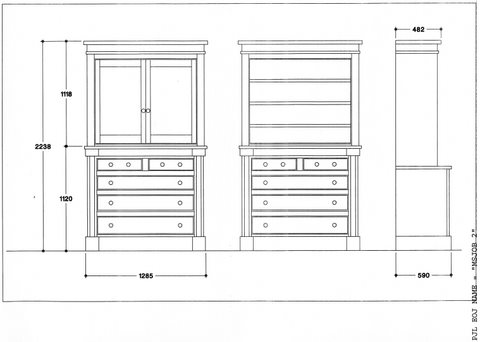
These are there to receive the proposed heel-blocks and pilasters as shown in the drawings.
However, during the inspection, my clients queried whether the item would benefit by their elimination.
This immediately indicated to me that they favour an even greater level of minimalism than I do myself.
But, since I had created the wide stiles for the purpose of receiving pilasters, not as a stand-alone design feature, I found it hard to see past this and expressed my doubts.
So I suggested that, to ensure that we achieved the best result, I apply mock-ups of both options, one to each side of the item, so that we could compare and contrast.
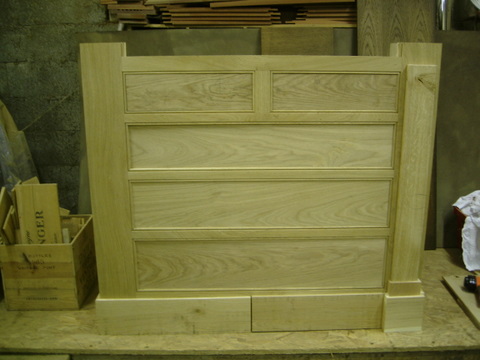
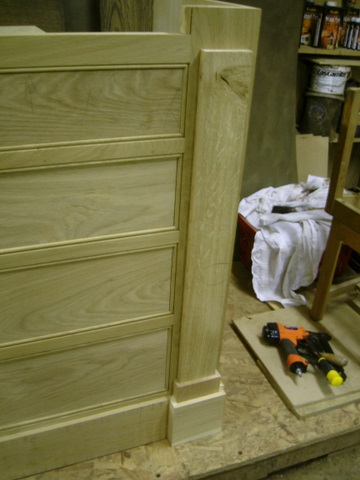
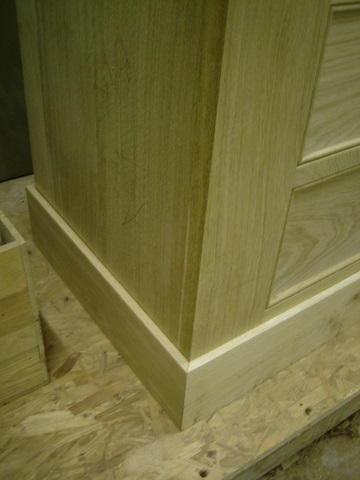
This I did yesterday and I came to the view that the elimination of the pilasters rendered the item too bland and I suspected that my clients might consider the skirting fitted round the heel-block too much.
So I decided to look for a middle way..........
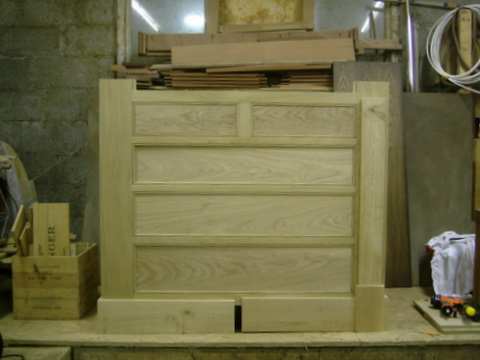
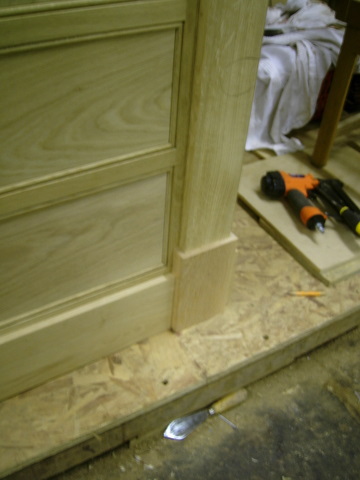
....................and came up with this.
And I sent all this up to my clients with the following comments...........
I think the skirting fitted straight on to the chest of drawers with no heel-block or pilaster is too bland or, in other words, I think the item looks better with the heel-block and pilaster.
But I figured that you might well consider the skirting fitted round the heel-block beneath the pilaster to be too fussy so I decided to look for a third way.
As soon as I had done it, it became my favoured solution.
Once your decision is made, I will refine the heights and margins of the elements: E.g the height of the heel-block relative to the skirting; the height of the skirting relative to the rail beneath the drawer etc., - for instance, if you were to select the original option of the skirting being fitted round the heel-block, there is far too much heel-block showing above the skirting.
It's over to you!
And I received their decision today.
They agree with me so we are running with the pilasters and the skirting running up to, but not round, the skirtings.
More soon.
The work on the Oak Gentleman's Dressing Cupboard is now well advanced.
At the outset of this post, which deals with the construction of the base, drawer section of the piece of furniture, I should say that I am very fortunate (and so, therefore, are my clients) to have the assistance of my colleague Martin Diack, who has excellent making skills and a 'good head'. (They train them well in NZ!)
We make a good team.
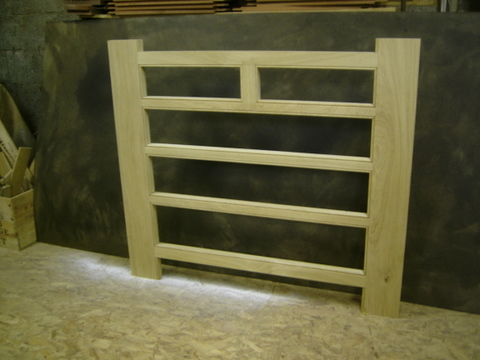
We started by making the frame with beaded-openings..........
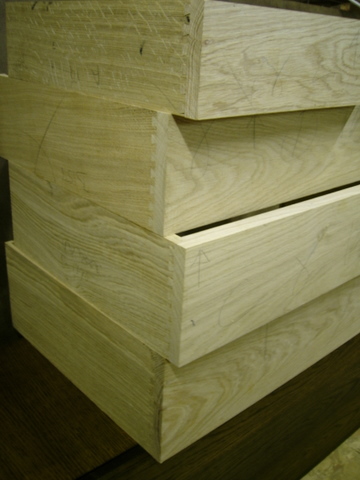
............so that we could cut the drawer-fronts to perfect size.
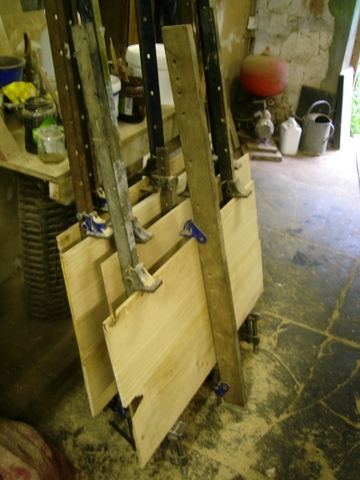
We glued-up the drawer-bases (from 18mm oak).........
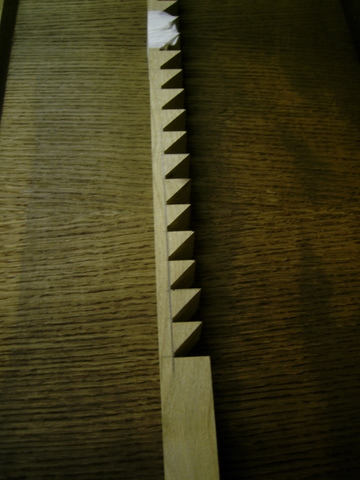
....... and Martin made the shelf-adjuster supports.
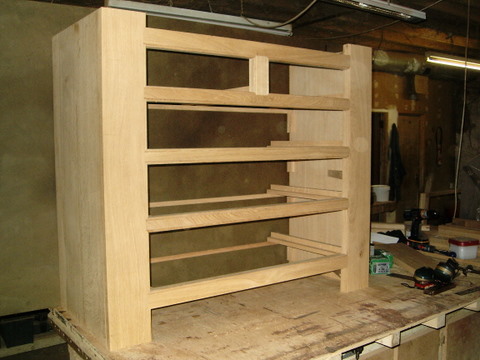
Our next step was to attach the gables................
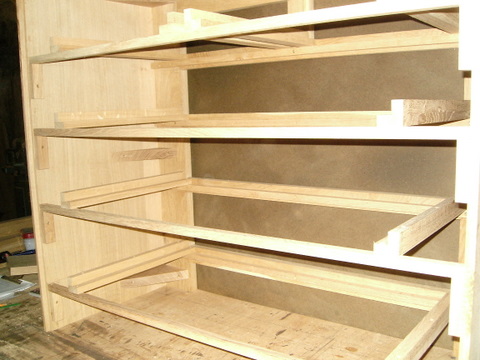
...............so that we could introduce the (traditional) drawer-runner system.
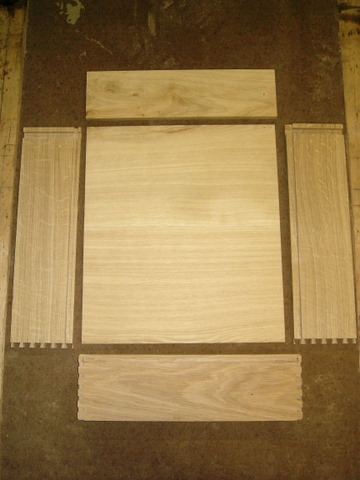
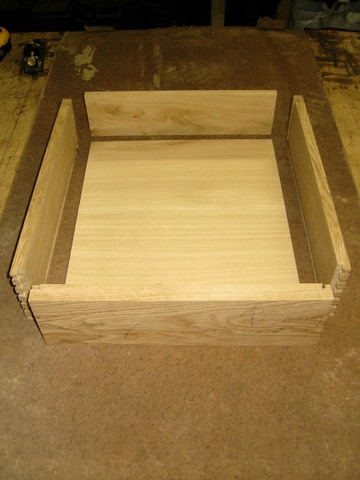
Drawer parts.
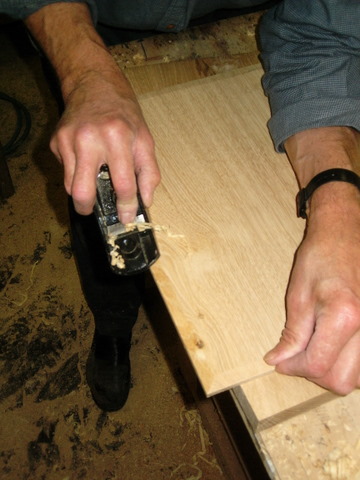
Fielding the underside of the, solid oak, drawer base..............
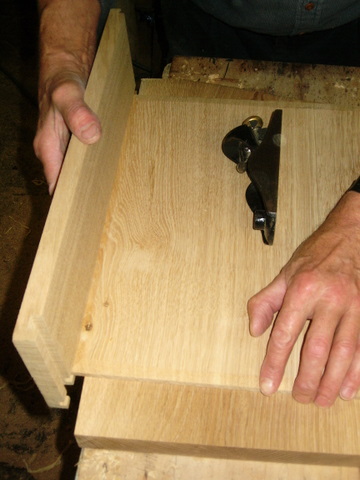
...............and testing the fit in a drawer side.
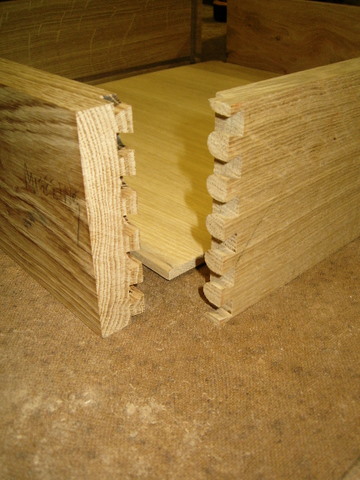
The dovetail pins and tails of a drawer front and side.
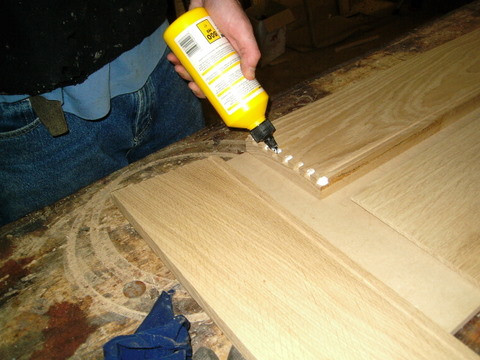
Gluing-up a drawer front.......
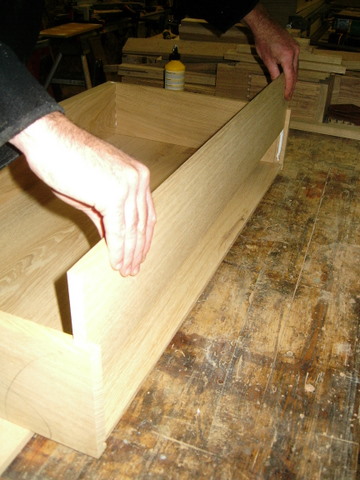
..............inserting a drawer back...........
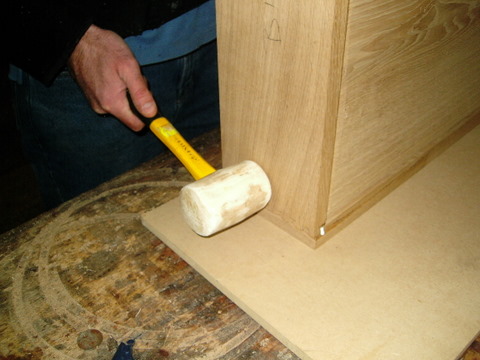
...........and assembling a drawer.

Drawers in cramps while the adhesive bonds.......
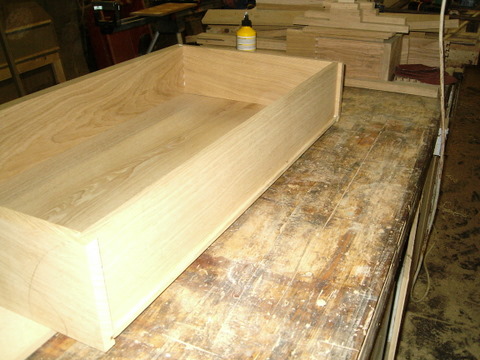
.......and an assembled drawer.
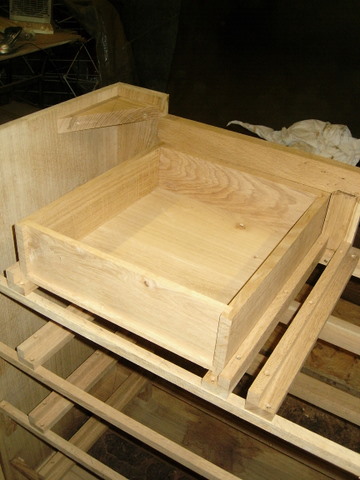
A drawer sitting in its runners before fitting.

Testing clearances while fitting a drawer.
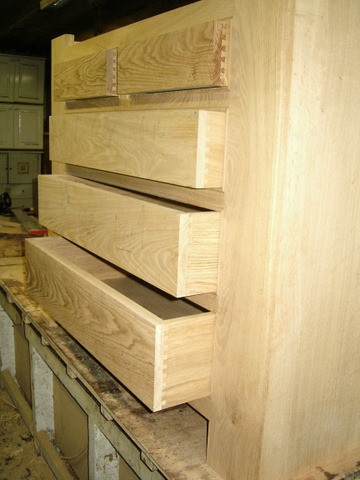
All the drawers fitted into their openings - or as we say 'opes'.
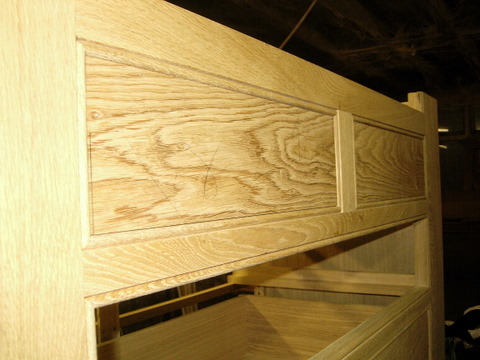
The top drawers fitted (note that they are cut from the one board so that the grain runs through both drawers.......
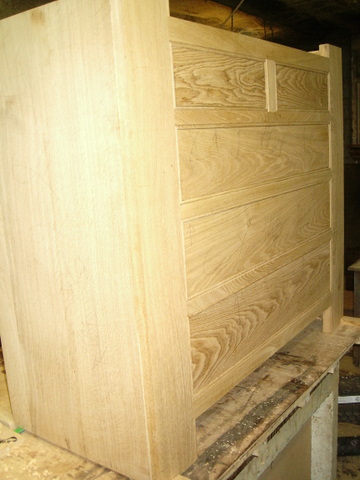
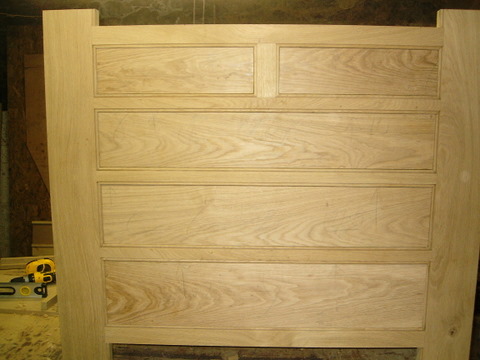
................and all the drawers fitted. (Note that the grain runs from right to left in the top drawers, left to right in the next drawer.....and so on down.
The next step is to build the upper, cupboard portion of the item.
Then, at the weekend there is to be a visit from the clients to view the work in progress.
I do hope they will be pleased. - I am!
Perhaps they will leave a comment?
As I mentioned at the end of part 1 of this tale, French oak has been selected for this commission.
And, as I also mentioned, I sourced it from Jean Hetier of The Art of Wood.
He stocks numerous grades of oak, including boules, as well as elm, walnut beech and maple.
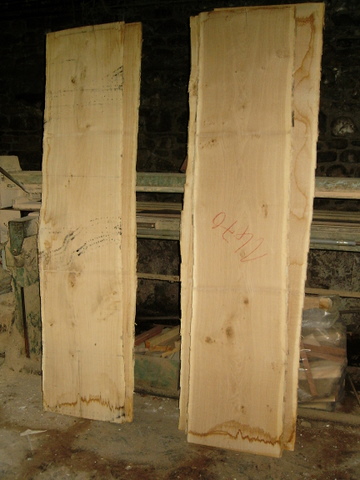
He carries oak up to 600mm wide including 18mm for drawer bases and backs.
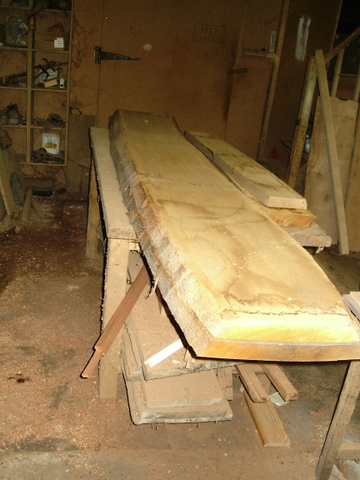
I was able to select 'bookmatched' boards for........
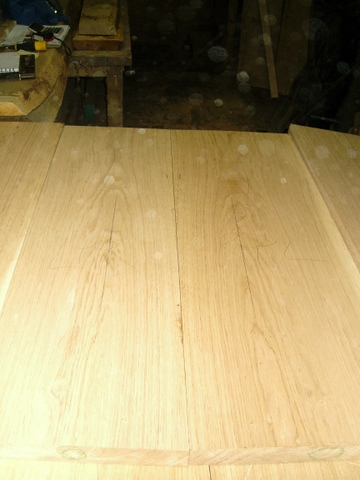
........matching the grain........
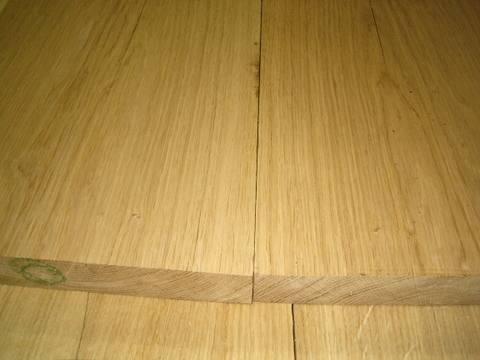
............for panels.
I have not been able to locate timber to these specifacations for years and, outside of my own brief efforts as a timber processor, never within Ireland.
So, before I continue with 'the history' I thought I should say that, in my view, Jean's stocks represent a very valuable resource for furniture makers.
In March of this year I received a telephone call from an old client.
(It's a funny expression 'old client'.
Like 'small farmer', which means the farmer (maybe of gargantuan proportions) of a small farm, 'old client' (who may be very young or, as in this case, certainly much younger than I am), is a person who has previously been a client).
Anyway, he asked me if I would be interested in quoting for designing and making another piece of furniture for him.
Of course I was interested - as I mentioned in the post 'Stirring Memories...........' 2 April 2010.
We met to discuss his requirement: A Gentleman's Dressing Cupboard or Press.
Now I had an immediate mental image of A Gentleman's Dressing Cupboard and, interestingly, it concurred entirely with what was in my 'old client's'
mind - A cupboard with low-fronted, sliding drawers behind a pair of meeting doors, above a chest of two short and two long drawers - and, indeed, he had a picture of just such an item to show me.
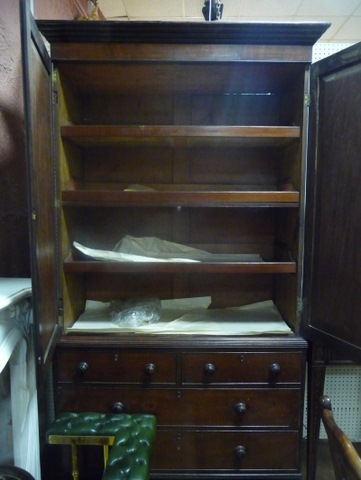
Once home, I checked in John Gloag's – A Short Dictionary of Furniture – to find no entry for a Gentleman's Dressing Cupboard. - Gentleman's Dressing Stand, see Dressing Stand has an entry, as do: Dressing Box; Dressing Chair; Dressing Chest; Dressing Commode and Dressing Stool.
And under an entry for Gentleman's Repository Mr. Gloag says: Term used by Ince and Mayhew in The Universal System of Household Furniture (1759-62) for a large piece of case furniture with a break front, shown on plate ........ In the explanation of the plates it was described as follows: 'The upper or Middle, is a Book-case, on each side is Draws, the Top of the under Part or Middle, is a Desk Drawer; under that either Draws or Cloaths-Press..... on each side is Cupboards.' Illustrations of such large pieces designed to perform several functions were probably included in the books of 18th-century makers, with the idea of starting trains of thought with potential customers, rather than as models to be executed.
And under a lengthy entry for Dressing Chest Gloag says: Alternative designs for a dressing chest with a superstructure of cupboards were given by Chippendale on plates........of the Director (Third edition, 1762), and described as a 'Dressing Chest & Bookcase.'
But anyway, at our first meeting (or rather, our first meeting for some thirteen years) we discussed the fine-detail of the requirement and, as set-out in my post What is Design or The 'Mission Statement' of a Commission Designer and Maker........ 26.03.10), I established who would be using it and for what purposes, inspected the site and assessed the adjacent features as to how or whether they should influence the design of the proposed item and how they would be influenced by its imposition in the space.
And our conversation ranged widely and my client (for so he has become) told me of his friendship with William Bunbury of the Lisnavagh Wood Project and his hope that, were the project to go ahead, the timber for it could be sourced from there.
So, with my head now filled with the information I required to start-out on the design process I decided, first, to contact William Bunbury at Lisnavagh to see if I could move forward on the materilas front also.
I had, indeed, long intended to visit Lisnavagh so this was precisely the impetus I needed.
Email to William Bunbury of Linavagh 25 March 2010
Good afternoon,
I am a furniture designer and maker and I have an enquiry for a
fine-furniture item from ****** ***** who is an old customer of mine
and, I understand, a friend of yours.
****** is hopeful that I will find timber that will suit this project
from you.
Neither ****** nor I are fixed on a particular species: quality, and
appearance will determine the selection.
I will need 1" and 1 1/2" material kiln-dried to 10%.
Would it be possible for me to visit you next Monday morning, March 29th.?
I used to be involved in kiln-drying hardwoods myself, so I really look
forward to seeing your operation.
Regards,
Clive Nunn.
Reply from William Bunbury 25 March 2010
Hi Clive,
Many thanks for your e-mail and it's great to hear from you.
I have been aware of your work for some time and also of your work with
Mickey Gabbett, who I know. I had a look at his (& your!) set up at
Ballaghtobin around nine years ago before I really got going here at
Lisnavagh with milling and drying our timber. It seemed so sad that your
idea had not worked out there, but it taught me to proceed with caution!!
I would be thrilled to show you around on Monday morning - it would be
interesting to see what you think of our set up! Would about 10.00am suit
you? I will introduce you to Dena Nolan and Bradley Richards who (these
days) are better able to help with details of our stock than I am.
Yes, I have known ****** ****** for some time and have a lot of time for him.
He was very helpful to me about 15 years ago when I was dabbling in music.
So I really hope that we can find something that might suit you both!
Let me know if 10.00on Monday suits you.
Best wishes
William.
(More in 'Stirring Memories................. 02.04.10')
Email to the client 30 March 2010
Hi ******,
As heralded, I visited Lisnavagh this morning and I could see just why you would want to source the timber for 'the item' from William. - Lovely people in an equally lovely place and he spoke just as warmly of you as you did of him.
But, assuming of course that I present a proposal that you decide to commission, it remains to be seen as to whether I will source any of the wood from him.
I certainly saw some good timber, especially oak, but I remain uncertain as to its viability for a fine-furniture item destined for a centrally-heated environment. - In fact, I definitely wouldn't use their material for the structure (framing): this only because of their drying method but, if you were to agree on oak, I hope that they would provide the 'glamour' as in, panels, gables etc., etc...
They are in something of a state of flux at present so I await their call to return to look at material that they have agreed to select from their stocks that meets my specification.
We shall see what we shall see and I'll keep you briefed.
In short, it looked to me as though making an Irish hardwood-processing enterprise 'work' has become no easier since my attempt!
Meanwhile I will get on with the design work, and the costing, so that we can proceed (or not) as soon as the materials issue is decided.
Best regards,
Clive.
Email from the client 30 March 2010
Dear Clive,
I have a great affection for William and am aware that he is very much swimming upstream in his various endeavours at Lisnavagh. The 18th and 19th century machine that is a landed estate is, I imagine, a supremely difficult one to run in the 21st century. However, love of place seems to be the motivating factor from him. And who could blame him? It is such a beautiful environment.
Regarding the wood, I will be completely guided by your advice and experience. If it was possible to include some of William's wood as the 'glamour' element that would be wonderful. However, if you do eventually decide that there is nothing suitable, so be it.
I am very glad that you have had the chance to meet with William and hope that there might be some other business that the two of you can do in the future.
I look forward hearing more from you soon.
Best wishes,
******
Email to the client 7 April 2010
Hello ******,
I have not heard back from Lisnavagh yet - of course it has been holiday-time - but my thoughts are beginning to take shape.
From what I saw there, I think it most likely that it will be oak for the panels that they may be in a position to supply.
So, I am thinking that I might use North American white oak (as in your dresser and dining table) for the structural elements (framing), for reasons of stability, and the more figured, Irish oak for the panels, sides, drawer-fronts etc..
As you mentioned, ******** **** **** is not necessarily the final position for the furniture items. So, although they would not currently be in the same space, it is possible that they would be in the future, so I thought it might make some sense if they were related in terms of both materials and design and this timber selection would be largely consistent with the oak wardrobe already in place.
What do you think?
I expect to be in Dublin one day next week when I would plan to meet with you to go over a preliminary proposal and give you a budget estimate.
How would this fit with your movements?
Regards,
Clive.
Email from the client 7 April 2010
Dear Clive,
That all sounds perfectly fine. Needless to say, please do not do too much prior to our having some idea of the budget. I don't want you to be disappointed if penury scuppers the plans.
We will be around all next week, so anytime is fine by me. The closer to 9am is best, as the kids are dropped to school and ***** will still be at home.
Best wishes,
******
Email to the client 12 April 2010
Good evening ******,
Sorry to pester you but if you got a moment to take a snap of the wardrobe for tomorrow morning it would be very helpful and would enable me to better focus my proposal to you.
Many thanks,
Clive.
Email from the client 13 April 2010
Dear Clive,
please excuse me but I have only returned to my desk this afternoon.
Here are two shots of the wardrobe. I hope they suit.
On a different note, attached is a shot of a pair of regency mahogany chiffonier from the mid 1830s that were made by my great, great grandfather (on my mother's side), Henry ***** (1801 - 1869), of ***** Street in Limerick.
It seems that a love of well made furniture runs in the family. Could any element of the design of the latter be incorporated into the new piece, no matter how subtle?
Best wishes,
******
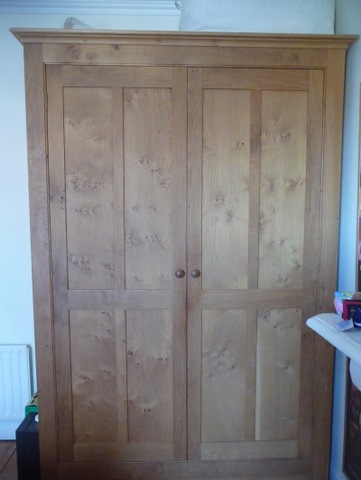
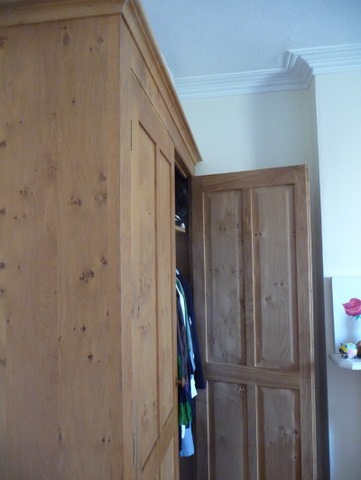
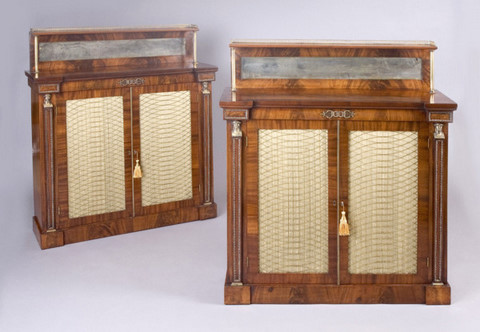
Email to the client 13 April 2010
Thank you very much ******, that's exactly what I wanted re. the wardrobe pics.
The chiffoniers made by your great grandfather are beautiful and beautifully made. Of course we could incorporate a detail from them into the 'proposed' item. First thought would be the columns but we can chat about that when we meet. - That now looks more like early next week rather than later this week.
I'll keep in touch.
Best regards,
Clive.
And we did meet when I showed my client drawings of a preliminary proposal with various door panel options.
We discussed them and I came away with the feeling that we were close to an agreed solution.
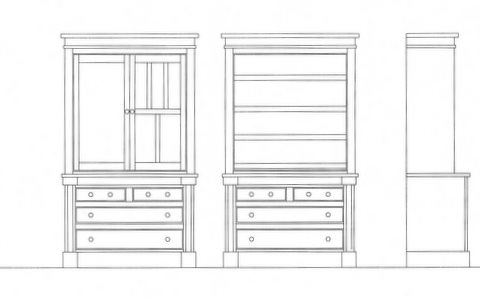
Email from the client 20 May 2010
Dear Clive,
***** and I have had a good discussion about the piece, and would like you to proceed with its making. We would like, however, to put a ceiling of €*,*** inc Vat, if you can work within that budget.
We also have one or two observations and suggestions. On the drawings that you have given to us, the depth of the base part is 608, which seems to bring the piece exactly flush with the wall depth of the adjoining built-in wardrobe. The skirting board would presumably push that out another centimetre or two. Would it be safer to drop that depth back to say 580 or 590? Also, would you consider raising the height of the bottom half of the piece from 900 to about 1120 to add one more row of drawers and take away on of the drawer/shelf levels in the upper part? Finally, and especially if this means less work for you, we would be happy to have shelves rather than the more traditional drawers in the upper part, as this area will be used mainly for the storage of sheets and blankest and would not be used, practically, as often as the drawers in the bottom section.
Your feedback will be deeply appreciated.
Best wishes,
******
(This email clearly highlights a flaw in all I have said so far concerning the progress of this project: I have refered throughout to 'the client' and 'my client' when, in truth it should be 'my clients'. It is just that, for logistical reasons, I have dealt with just the one party.)
Email to the clients 21 May 2010
******, thank you very much.
Yes, of course I can work within that budget, especially with the elimination of the upper drawers.
I am really delighted and grateful, not just for the business which is of course very welcome, but I really like the item and it is a true pleasure to work for and with someone that takes such an interest in the whole process of bringing an idea through all the stages to production. It fully vindicates the function of being a commission designer and maker if one can successfully reconcile the three elements of the need and purpose to the function and the space and position.
Yes, we will certainly adjust the depth so that all of the item is within the depth of the adjacent cupboard.
I am less certain about altering the relative heights of the upper and lower portions.
First reaction and gut feeling is that it may destroy the proportions of the item.
So, over the weekend, I will redraw the item to your suggested dimensions and email the result to you, along with my opinion.
Once we have settled these final details I will ask you for a deposit so that I can start to assemble the materials before I go to Canada on 4 June in readiness for starting work on my return on 18 June.
In this connection, I received a telephone call from ******* yesterday when he said that he may have some suitable oak for me to look at - but then again he wasn't sure! We shall see what we shall see.
Keep your eye on your email, from lunchtime onwards tomorrow, for the amended drawing.
Thank you again.
Clive.
Email to the clients 22 May 2010
Good morning ****** and *****.
I attach the amended drawing. I have only adjusted the left hand image with doors, so that you can contrast the new proportion against the right hand original proposal.
My opinion? Yes, I do think that the original proportion is more pleasing but not to the extent that I would fight against the change.
I think the decision should be yours: you know the extent to which having another drawer will improve the function of the item and only you can decide if that benefit outweighs any disimprovement to its appearance: that is, of course, if you share my view that the appearance is compromised.
I did not take the time to re-calibrate the drawer sizes: I would, of course, do so if we go with the extra drawer. By this I mean the deepest drawer would be at the bottom and they would be graded as they go up.
So its over to you and I look forward to hearing your decision.
I'm off to cut grass on a perfect summer's morning!
Best wishes.
Clive.
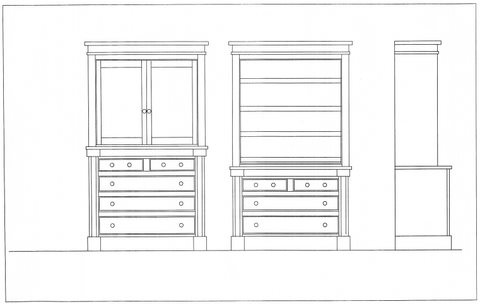
Email to the clients 31 May 2010
Good afternoon, ******,
Thanks for passing-on your decision and I will of course ensure that it looks its best.
I will be in Dublin on Wednesday when, if it is convenient, I will call by to give you the final drawing with the drawers properly configured and to have a last word about the material.
It would also give me the opportunity to check again the available height: it may be that we could steal an extra few centimetres.
I would also be grateful if I could collect the deposit cheque: I'm hoping that some of the basic framing work will be done while I am in Canada.
I will call you tomorrow to check if this works for you.
Thanks again.
Best regards,
Clive.
Email to clients 8 June 2010
Good morning from Canada.
I'm sorry In did not get these to you before I left but, foolishly, I mislaid where I had noted *****'s email address and anyway I ran out of time to get all I needed to do done.
Anyway, here are the amended drawings for your consideration and approval.
As you can see, I am on email here so feel free to contact me if you wish though we are going to be in the Rockies from tomorrow until the following Tuesday where I doubt that I will have a connection.
Anyway, I will be in contact immediately upon my return on 19 June and, once any last minute refinements are agreed, I will get into full production.
Best regards,
Clive.
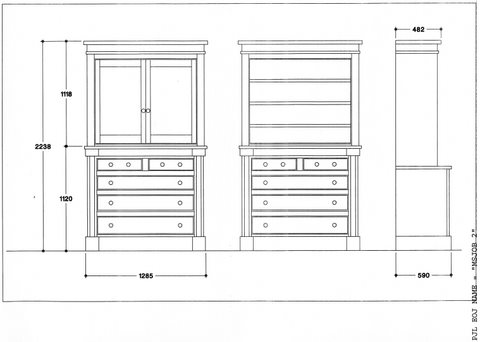
Email to clients 21 June 2010
Good afternoon, ******,
I'm home and getting my feet back under the table after a truly wonderful trip to Canada.
Would it be convenient for us to meet on Wednesday or Thursday to go through the final, final details and for me to collect the deposit with a view to my getting into full production on Monday 28 June?
I will give you a call tomorrow.
Best regards,
Clive.
And we did meet on the Wednesday when we agreed the final minor details.
And at this meeting I asked my client if he would be amenable to my 'blogging' the story of his commission from start to finish. And to my delight he agreed without demur.
I returned home, prepared the first working drawings and got on to Lisnavagh to see if I could finalise the materials requirrement.
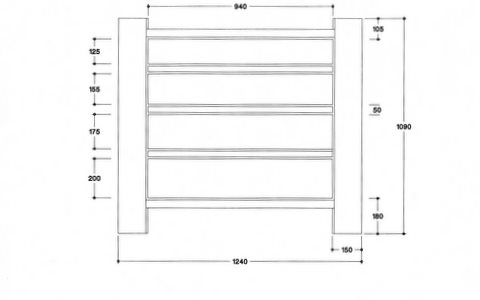
Sadly, I was unable to source timber that I considered suitable for the item at Lisnavagh and it will now be made from French oak, sourced from from Jean Hetier, of The Art of Wood, who holds substantial stocks on the Kilkenny to Kells road.
And so, fully four months since my client's telphone enquiry 'the item' will go into full production tomorrow, Monday 19 July.
In fact, considerable progress has already been made because, as I mentioned, I had taken an early decision that the 'structure' would not be made from Lisnavagh oak even if they could supply material for other parts. Thus, having discovered the local French oak resource and having satisfied myself as to its suitability, I purchased the structural material there and the framing is already complete.
And although I am sorry that it will not be Irish oak from Lisnavagh, as my clients had hoped, I am pleased that the piece will be made from the one material, from the one source.
As you can see that this furniture commission had a considerable 'history' before any wood dust was created, so to speak.
From here onwards I will show its progress with with but few words and many visuals.........
A chair has more demanded of it than any other item of furniture.
Leaving considerations of design, beauty or elegance aside for the present, a table needs only to be stable enough for its function; a cabinet may have doors and drawers that must operate efficiently and repetitively but otherwise has only to sit in the one place.
But a chair, and I am thinking here of dining chairs or chairs that are used at a table, desk, work-station or similar, must be comfortable - comfortable over a period of perhaps many hours of being sat on, and above all, be strong, and very strong, without being heavy.
Think about it: a dining chair must, each and every time it is used, be capable of being moved back (dragged) from the table, sat on and then, with its occupant's weight upon it, moved (jerked) forward into the desired position relative to the table.
The seated person will then move constantly, redistributing their weight in a manner that may test every joint of the chair: and it must be capable of having this done to it again and again and again, thousands and thousands of times over its lifetime, without showing any sign of the stresses that it has endured.
Now, for the commission furniture maker of once-off items such as myself, this poses problems.
Consider a commission for a wooden table and six wooden chairs.
The simplest table is likely to have nine components while the simplest chair will have a minimum of ten components.
So, in numeric terms, there is more to making one of the chairs than there is in making the table. - Table, nine components; six chairs, sixty components.
Consider these facts in the context of the cost / benefit for the client and then apply the same calculation from the maker's perspective.
Let us say that the table attracts 2.5 units of cost.
Experience informs me that this cost / benefit calculation is most often met with equanimity and acceptance by the client: from the client's perspective, it seems, a large item can sustain a large price.
Now, clearly, the volume of material required for the table is vastly greater than the volume of material required for a chair, or even six chairs.
But the cost of converting, accurately (and for the reasons indicated above accuracy for chair components is an imperative) a large number of small components is greater than converting a smaller quantity of large ones.
So, from the makers perspective, the unit of cost of one chair should, rightly, be at least that of the table.
But to present a potential client with an estimate of 2.5 units of cost for one chair would be met with alarm, consternation and certain rejection because, wise as all clients are, they spot that the cost for six (small) chairs would be six times greater than the cost of the one (big) table.
Again experience informs me that to present a client with an estimate of even .5 units of cost is still met with resistance and most often rejection.
So where does this leave the proposed contract?
In my case, having explained the rationale for the high cost of once-off, hand-made chairs I offer two solutions.
I offer them a chair of my design that I have batch produced by a chair maker which I can sell-on at just below .5 units of cost by taking no margin myself.
In other words, the chairs are a loss-leader for getting the commission for the table!

Batch produced Stick-back Chairs, of my design, in use in our
own home.
Or I encourage the customer to try to find a mass-produced chair that they like, the unit cost of which will be small fraction of mine as a consequence of the economies of scale in its production. (I have seen many an acceptable chair offered for sale at a price that is less than the cost of the materials if I were to make it.)
And I do not believe that this difficulty surrounding making chairs at an affordable price is a circumstance or situation.
Furniture making and chair making are plainly not mutually exclusive activities but since the eighteenth century, at least, chair making has, increasingly been separate from general furniture making for the very reasons I outline above.
Chairmaking became, I suspect, one of the first examples of mass-production.
The chair maker developed a number of designs to complement the prevailing furniture styles of the day, that could be made in large numbers and offered to the emerging retail furniture trade.
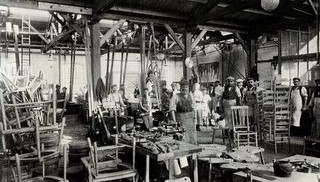
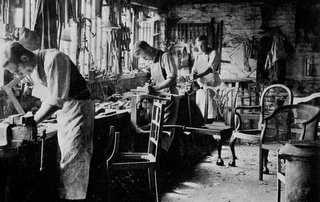
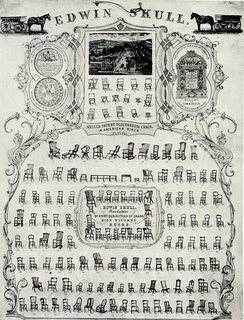
What is Design? or The 'Mission Statement of a Commission Designer and Maker
As a designer and maker of furniture I am asked from time to time 'what are the favourite items of furniture that you have deigned and made?'
I'm not very good at favourites - of anything - be it person, book, film, meal, wine etc., etc., let alone furniture.
In all these instances - and others - I'm inclined to see things in their context, especially so when it comes to furniture items for the design and execution of which I am responsible.
This leads me to what I consider to be the 'fundamental of design' and the very essence of my work and business.
As I'm sure I will have mentioned, I am a 'commission' designer and manufacturer which means that I do not make a product: instead I respond to the needs of potential customers, places and spaces.
Invariably the first step, to follow an enquiry, is a visit to the potential client in the space for which the proposed furniture item is intended. - In fact I will not proceed without this step having been taken because, without it, I am in an information vacuum.
This 'on site' meeting enables me to seek to understand more fully what is in the enquirer's mind; to assess the place, position and space for which the item is intended; fully appraise myself of the function or functions that it is to fulfill and inform myself of any other factors that could or should influence the design.
I really don't, and cannot, conceive ideas until I have this information in my mind and often, even once I do have it, some time passes before I begin to perceive or formulate a solution.
From time to time, though not very often, I don't come up with a solution that satisfies me - and if I cannot satisfy myself there is small prospect of me satisfying the customer so, on these rare occasions, I have no difficulty in informing the potential client that I am not the designer for the project.
But to get back to the notion of 'favourites'.
My 'favourites' are 'moments or occasions' rather than 'particular objects'.
It is when I believe that I have achieved a truly satisfactory fusion of the factors that lead to the design and execution of a piece of furniture.
These factors are:
to understand and interpret the client's ambition in visual terms
to match this aesthetic to the intended function of the artefact
and
ensure that the object compliments, or is complimentry to, its position and surroundings
So, it is when I consider that I have achieved this in the creation of an object and, more importantly, when I believe that my client fully shares my view, that a 'commission' will be a 'favourite'.
Now, in that formula for success, the hypothesis exists that I may not particularly like the result myself because it is not me that I am seeking to satisfy.
It also means that it may as easily be an humble object of small (financial) worth, as a 'major opus'.
But, as with all rules, there are the exceptions that prove them.
One such, is to work 'off the drawings' of a building or space that has yet to be created.
To be in at the beginning of an idea or project, the outcome of which you may have the chance to influence or improve, has the potential to provide the greatest creative stimulus.
I have already blogged one such experience which I reproduce below.
I had the good fortune, some years back, to design and install the fittings for an entire house that was then in progress.
My involvement started with an enquiry for a single item, what that was I forget but, most likely, it wil have been for the kitchen.
However, by completion we had supplied not only the kitchen but also the front and all the internal doors, the architraves and skirtings, the units in the bathrooms, the study, flooring and the design for the stairs.
It is not often that one is given the opportunity to provide so many elements into one space at the one time and, thus, be in a position to influence and co-ordinate their design and the materials. (The timber, in this instance, was Spanish Chestnut grown in Ireland and supplied from the timber company during its short commercial life. (See - The Timber Drying Experiment... 21.11.09).
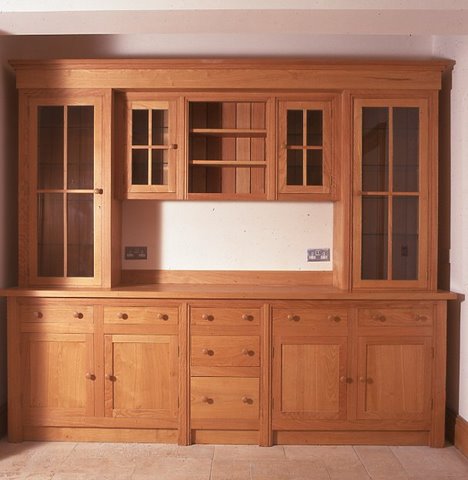
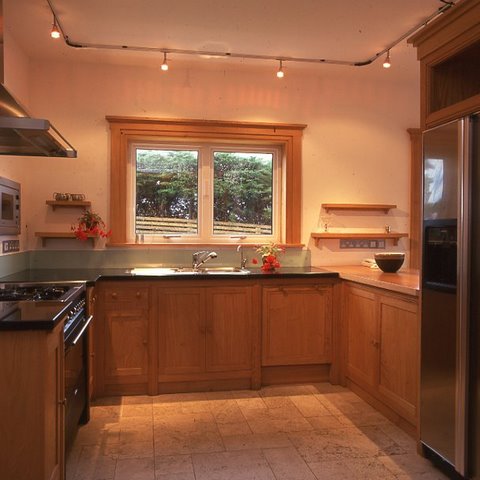
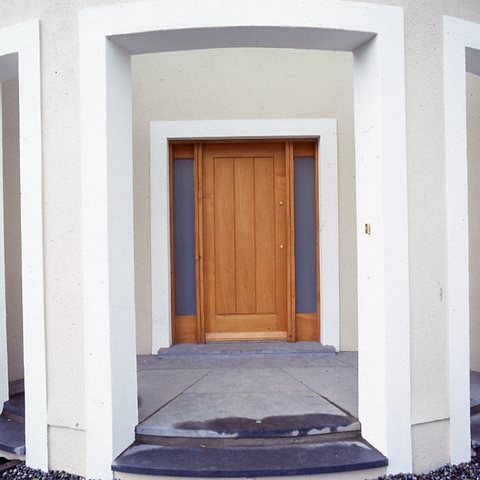
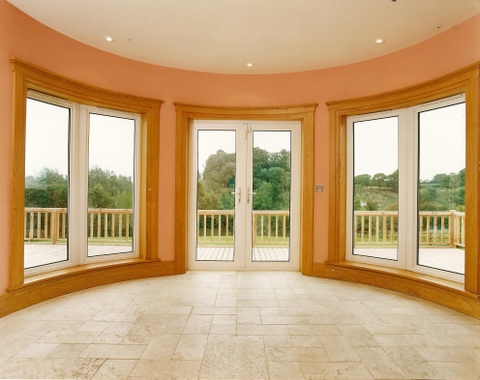
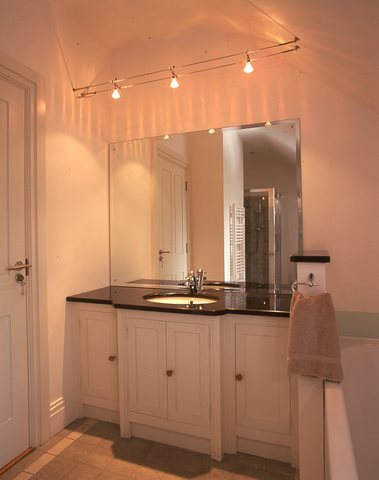
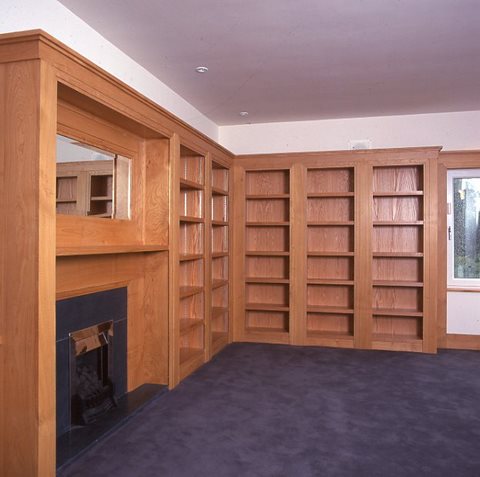
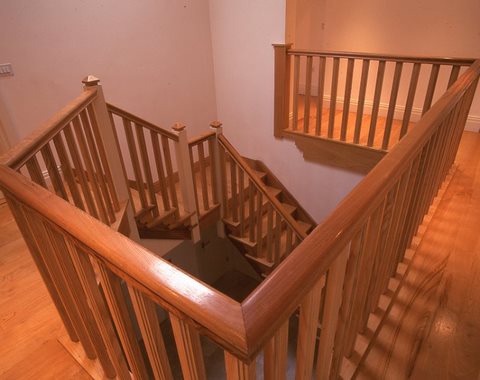
I wish I could name my clients because they were enormous fun to work with. - But I can't. - Their circumstances changed and they moved-on before they had the chance fully to occupy their creation.
And I do not know the current owners.
So, for the one reason and the other, I do not feel free to name names or to locate the house more specifically than its county.
However, if my clients were to happen upon this entry, I hope and trust that they will have similar, positive memories of our working together and, equally, if the currrnet owners were to do so, I hope they will not feel intruded upon.
(End Kilkenny House)
Another exception, is the creation of the limestone table that I described in (Kilkenny Limestone 16.11.09) part of which I also reproduce here.
all posts »